Since Dupont began producing PTFE in 1945, it has been 61 years since. Now as an important product of PTFE PTFE microporous film is widely used, expanding the field from biological engineering to garment industry, from mechanical industry to petrochemical, in the environmental protection industry can be used not only for water treatment projects, but also for air particle purification. It can be said that its application range is still relatively wide.
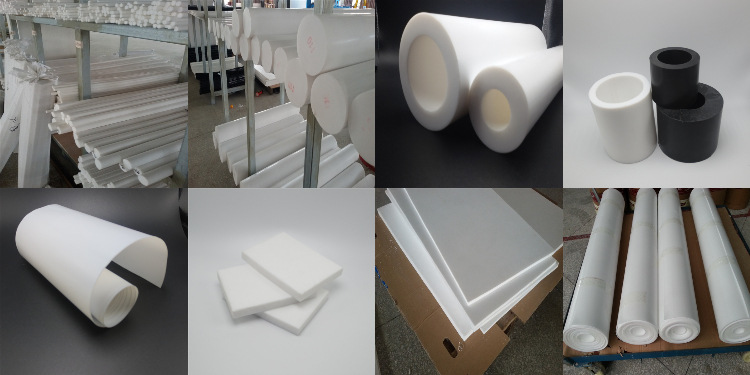
Characteristics of polytetrafluoroethylene
1. Molecular structure characteristics
2. Chemical stability
3. Thermal properties
4. Mechanical properties
5. Electrical properties
6. Surface properties
Development of PTFE microporous film
At present, the production process of PTFE microporous film has calendering film method, turning film method and stretching film method. Stretch film method can be divided into one-way stretch and two-way stretch, through structural analysis and actual measurement, only two-way stretch film has good microporous structure. The production process of biaxially oriented PTFE microporous film is shown in the figure.
Application of PTFE microporous film
1. Application in filtration materials
2. Application in medical materials
Preparation of PTFE film
1. Pre-process of PTFE microporous film
2. Preparation process
3. Production process
The influence of operating parameters on the properties of PTFE films
The factors influencing the properties of PTFE microporous films in the biaxial stretching process and its pre-process are complex and multifaceted. In addition to the performance of the processing equipment, stretching temperature and stretching rate, other influencing factors are: operating temperature, operating humidity.
Operating temperature: PTFE films are particularly sensitive to temperature, and different operating temperatures can result in different film properties. Temperature is a critical operating parameter not only in the stretching process, but also in PTFE resin processing and intermediate processes.
Operating Humidity: Humidity is temperature-dependent and cannot be discussed without temperature. Ambient humidity also has an effect on the film.
PTFE has outstanding chemical stability, excellent high and low temperature performance and corrosion resistance, and is widely used in chemical, petroleum, textile, electronic and mechanical industries. Meanwhile, the strong hydrophobic and porous properties of PTFE make it an ideal membrane material for the preparation of waterproof and breathable textile fibers as well as membrane distillation and membrane contactors. Compared with other membrane materials, ePTFE membrane is the only membrane that can be used stably for a long period of time with high mass transfer coefficient, and the advantages of small size, strong self-supporting ability and high loading density of hollow fiber membranes make PTFE hollow fiber membranes attract much attention in the field of membrane contactors.
Porous PTFE hollow fiber membranes are prepared by extrusion-drawing method, and the preparation process includes mixing, extrusion spinning, unidirectional stretching and sintering. The fully mixed PTFE material is pre-pressed on a blank press to make a cylindrical blank. The pre-pressed blanks are extruded and spun at 40-100°C. After degreasing, heat-setting to obtain PTFE hollow fiber membrane. The degreasing temperature is 200-340°C, the heat setting temperature is 330-400°C, and the heat setting time is 45-500 s. The microscopic form is a nearly circular (elliptical or circular) pore structure.
Post time: Jan-18-2022